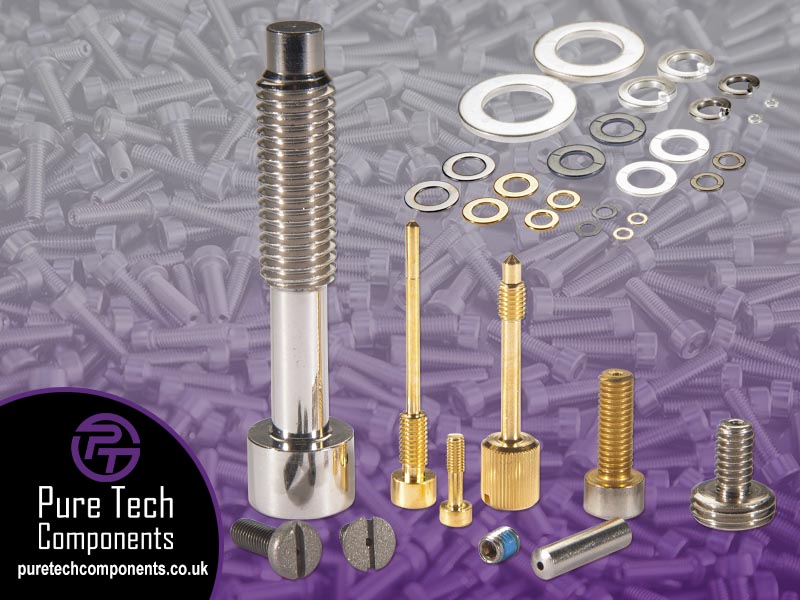
Fasteners are often an unnoticed, yet integral, part of any application that most people don’t give much consideration to until they need to use one. The material the fastener is made from is equally as important as their size specifications. Fasteners can be manufactured from a wide variety of materials and further enhanced by a range of coatings, platings, and finishing treatments. No matter what type of fastener you need – screw, peg, rivet, bolt, clamp, etc. – selecting the proper material for the intended application is critical to both performance and reliability.
In order to select the proper material for a fastener numerous factors need to be taken into consideration. There are four main criteria that need to be evaluated in order to select the proper fastener material. Those are:
- The load or stress
- Strength
- Resistance properties
- Temperatures
The load or stress
When selecting a material to fabricate your fasteners from you must take into consideration the proof load, the yield strength, and the tensile strength of the particular material.
- The proof load, or stress, is measured in pounds per square inch and refers to the minimum acceptable load that the fastener will withstand. When it comes to fasteners, pure steel, and low carbon steel have the lowest acceptable proof load.
- The yield strength refers to the load at which the fastener will become permanently deformed.
- The tensile (or ultimate) strength refers to the load that will break the fastener.
Strength
The strength properties will be very different depending on which type of material is used to create the fastener as well as the final shaft length of the fastener, plus a few other considerations.
Typical metal strengths at room temperature:
Material | Ultimate/Tensile (ksi) | Yield Strength (ksi) |
Inconel 718 | 210 | 175 |
Monel K500 | 160 | 110 |
Moly | 158 | 130 |
Titanium Grade 5 | 148 | 138 |
Inconel 625 | 144 | 84 |
Tungsten (99.5%) | 142 | 109 |
Super Duplex 2507 | 125 | 82 |
Duplex 2205 | 110 | 80 |
Tungsten Alloy | 94-100 | 75 |
Molybdeum | 94 | 90 |
Inconel 600 | 93 | 37 |
Zirconium 705 | 89 | 73 |
Aluminum 7075-T6 | 83 | 73 |
Monel 400 | 83 | 32 |
Titanium Grade 2 | 70 | 50 |
Nickel 200 | 60-85 | 15-45 |
Zirconium 702 | 68 | 47 |
Typical polymer strengths at room temperature:
Material | Ultimate/Tensile (psi) | Yield Strength (psi) |
PEEK (extreme) | 47900 | 51000 |
PEEK (glass fiber) | 22800 | 26000 |
PEEK (unfilled) | 16000 | 13600 |
Vespel | 12500 | – |
Torlon PAI | 22000 | – |
PVDF | 5000-8000 | 6500-8000 |
PTFE | 3900 | 1450 |
PFA | 3600 | 2000 |
Typical ceramic strengths at room temperature:
Material | Ultimate/Tensile (ksi) | Yield Strength (ksi) |
Zirconia | 75 | – |
Alumina | 30 | – |
Resistance properties
Corrosion wears metal down due to the material’s interaction with chemicals in the surrounding environment. The most common type of corrosion is oxidation, which is caused when the metal reacts to oxygen and rust. Typically to combat corrosion, the fasteners will need a protective coating applied such as chrome or zinc. Otherwise, if applicable, the fastener could be manufactured from a material that does not corrode such as non-ferrous metals or plastic alloys.
Temperatures
You need to take into consideration the average temperatures that the fastener will be required to operate in to be sure that the material can handle it. Obviously, plastics and non-ferrous alloys have no place in environments with extremely hot temperatures. Others can become brittle in extreme cold and lose their ductility.
What are the most common materials used to manufacture fasteners?
Here is a quick list:
- Metals, such as: Aluminum, Brass, Steel, Titanium, Magnesium, Molybdenum, Monel, Inconel, and many more.
- Polymers, such as: Nylon, PEEK, PFA, PTFE, PVDF, Torlon, Vespel
- Ceramics, such as: Alumina, Zirconia, and more.
What material would be best to select?
Fastener materials are typically selected based on their mechanical properties, potential for post-fabrication treatments, cost-efficiency, and a few other considerations. However, which material would be best for your application truly depends on what you need the fastener to join and where. In critical applications that will be exposed to extreme temperatures or corrosive environments, it is best to select a material that is strong, can withstand the temperatures, and has good corrosion resistance.
Aluminum
Aluminum is a very popular and affordable material choice that provides manufacturers with a lot of versatility. Alone it is a great choice for lightweight, lower-strength, applications that need the material to have good resistance to corrosion. If combined with other metal alloys, aluminum can have the strength of steel but with a fraction of the weight.
Brass and Bronze
Brass, an alloy of copper and zinc, is the most common copper-based alloy used to manufacture fasteners. It provides decent resistance to corrosion, is relatively inexpensive, and has good electrical conductivity properties. Bronze, an alloy of tin and copper, boasts very high corrosion resistance. Both of these offer an attractive reddish-yellow color.
Steel
Steel is a popular fastener metal and comes in a wide variety of forms and strengths such as alloy steel, carbon steel, stainless steel, and many more. The corrosion resistance properties and mechanical strength of steel makes the material incredibly desirable for fasteners. The mechanical strengths range from approximately 50ksi (kilo-pound per square inch) to up to 300ksi.
Titanium
Titanium is one of the best choices for fastener manufacture, especially for high-impact applications. It provides low weight, a high level of strength, as well as incredible resistance to both corrosion and wear.
Polymers
Engineered Polymers offer unique properties for specialty applications. Their temperature limits typically range from 100° C to just under 600° C. They also provide good corrosion resistance and offer decent tensile strength.
Ceramics
Few materials can withstand heat, pressure, and corrosion better than ceramics. However, they are not typically very strong; over-torque them a tiny bit and they will shatter. This makes them tricky to initially install which turns most people away from them.
Here is a quick reference table of the most commonly used fastener materials and their most notable properties:
Aluminum | Brass or Bronze | Titanium | Nylon |
-Light -Soft -Corrosion resistant | -Relatively soft -Corrosion resistant -Electrically conductive -Aesthetically pleasing | -Superior strength -Extremely corrosion resistant -Ideal for high-temp. environments | -One of the most commonly used plastics -Exceptional strength -Excellent wear resistance |
Steel – Alloys | Steel – Carbon | Steel – Stainless | Ceramics |
-High strength -Low corrosion resistance -Often brittle or rigid -Often requires additional coating | -Grades 2, 5, and 8 are standard for bolts and screws | -Superior strength -High corrosion resistance | -Good strength -Extremely corrosion resistant -Survive extremely high temperatures -Non conductive -Non magnetic -Lightweight -Reuseable |
Even the smallest component can ruin the effectiveness of a product or cause significant challenges, which in turn may determine a manufacturer’s success or failure. By partnering with experts like us in engineering and supply, manufacturers not only solve potential issues before they arise, but also boost safety, quality, speed to market, and profitability.
How can we help you?
Pure Tech Components is the premier UK distributor for UC Components, Inc. RediVac® line of fasteners, washers, hex nuts, and O-rings. We provide only the best specialised fasteners to a wide range of industries, including medical, food processing, optical, vacuum, semiconductor, and R&D. Partnering with us gives you the confidence and reassurance you need to concentrate on your customer’s needs without worrying or compromising on cost, quality, or customer service. Contact us today for more information or to place an order.